Plastik enjeksiyon
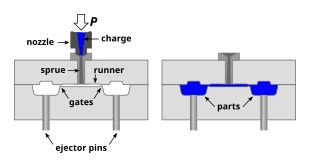


Plastik enjeksiyon, temelde kapalı bir kalıbın içine plastik malzemenin eriyik sıcaklığının üstündeki bir sıcaklık aralığında yüksek hızda yolluk girişinden kalıp gözüne hızlı bir şekilde enjekte edilmesi sonrası, ütüleme fazı ve tutma fazı ile parçanın boyut ve görsel toleranslarının kabul edilebilir seviyeye getirdikten sonra plastiğin kalıptan çıkma sıcaklığının altına getirilerek kalıptan çıkarılması prensibine dayanan bir plastik parça imalat yöntemidir. Seri üretime uygun olması sebebiyle, birçok sektörde oldukça fazla kullanılan bir üretim yöntemidir. Bu metot ile en küçük komponentlerden, otomotiv, savunma sanayi ürünlerine kadar çok çeşitli ebat ve kategorilerde plastik parçalar imal edilebilir.
Plastik enjeksiyonun avantajlarını aşağıdaki şekilde sıralanabilir;
- Düşük maliyet
- Otomasyona uygunluk
- Son işleme prosesine ihtiyaç duyulmaması
- Yüksek hızlarda üretim
- Farklı yüzey, renk ve şekillerde parça üretimine uygunluk
- Malzeme kaybının çok az olması
- Aynı kalıpta farklı ürünlerin üretilebilmesi
- Düşük toleranslarda çalışabilme
Plastik enjeksiyon karmaşık olmayan bir yöntemdir. Plastik enjeksiyon yöntemi, kalıbın plastik enjeksiyon makinesine bağlanması ve granül veya toz halindeki ham maddenin huniye beslenmesi ile başlar. Ardından ham madde ısıtılarak ergitileceği kovanın içine aktarılır. Kovan içindeki ergimiş haldeki ham madde belli bir basınç altında nozülden geçirilir. Ardından kovana göre daha soğuk olan kalıba, kademeli olarak değişen basınç altında ergitilmiş ham madde kalıba iletilir. Bu esnada ham maddenin kalıp içerisinde belirli bir süre soğuması beklenir ve şekillenmiş ürün kalıptan robot veya el yordamıyla alınır. Ürün alındıktan sonra proses tekrar başlar.[1]
Plastik Enjeksiyon Makinesi
Plastik enjeksiyon işleminin gerçekleştirildiği makineye plastik enjeksiyon makinesi denilmektedir. Amerikalı mucit John Wesley Hyatt, kardeşi Isaiah ile birlikte 1872'de ilk plastik enjeksiyon makinesinin patentini aldı.[2] Bu makine, günümüzde kullanılan makinelere kıyasla nispeten basitti. Plastiği ısıtılmış bir silindirden kalıba enjekte etmek için bir piston kullanmaktaydı. Endüstri yıllar içinde yavaş yavaş ilerledi ve yaka askıları, düğmeler ve saç tarakları gibi ürünler üretti.
Alman kimyagerler Arthur Eichengrün ve Theodor Becker, 1903'te selüloz nitrattan çok daha az yanıcı olan ilk çözünür selüloz asetat formlarını icat etti. Bu sayede, enjeksiyonla kolayca kalıplanabilecek bir toz form sağlanmış oldu.[3]
Arthur Eichengrün 1919'da ilk enjeksiyon kalıplama presini geliştirmiş ve 1939'da plastikleştirilmiş selüloz asetat enjeksiyon kalıplama patentini almıştır.
Plastik enjeksiyon makinesi temelde 4 ana bölümden oluşmaktadır. Bunlar;
- Enjeksiyon Ünitesi
- Kalıp Ünitesi
- Mengene Ünitesi
- Kontrol Ünitesi


Plastik enjeksiyon makinesinin tek başına yeterli olmadığı durumlarda, makineye ilave yardımcı ekipmanlardan destek alınmaktadır. Yardımcı ekipmanlardan en önemlileri:
- Sıcak yolluk kontrol üniteleri
- Kurutucu ve Dozajlayıcı Sistemler
- Şartlandırıcılardır.
Enjeksiyon Ünitesi
Plastik enjeksiyon makinesinin bu bölümde granül veya toz halindeki ham maddenin ergitilmesi sağlanır. Bu ünite huni, vida, ısıtıcılar, çek-valf, enjeksiyon memesi, hidrolik silindir ve hidromotordan oluşur.
Ham maddenin düzeni bir akışta kovana aktarılması huni tarafından sağlanır.
Vida ise ölçme, sıkıştırma ve besleme işlemlerinin yapıldığı 3 farklı bölümden oluşur. Ölçme bölümünde kuleden vidaya aktarılan hammadde oran belirlenir, sıkıştırmada hammadde istenilen derecelerde ergitilir, beslemede ise ergimiş hammadde kalıba aktarılır.
Çek-valfi ise sonsuz vida mekanizmasının ucuna takılan bir aparattır. Bu aparat, ergimiş olan hammaddenin geri akmasına izin vermez. Ayrıca vidanın bir piston gibi hareket etmesini sağlar.[4]
Kalıp Ünitesi
Eriyik plastik hammaddeye parçanın seklini verdikten sonra katılaştıran bir "takım"dır.Parça geometrisini oluşturan kalıp boşluğudur, bu boşluk da erkek ve dişi olmak üzere iki temel parçadan oluşur.Bu parçalara ek olarak parça tasarımına ve isteğe bağlı olarak yolluk sistemini oluşturan manifolt plakası, maçalar vs. bir kalıpta bulunabilen diğer parçalardır.
Enjeksiyon tezgahından kalıp boşluğuna eriyik plastiği getiren bir yolluk sistemi mevcuttur. Parçayı hızlı ve dengeli katılaştıran, sağlıklı bir ısı transferi gerçekleştiren bir soğutma sistemi gereklidir. Parçanın kalıptan ayrılmasını sağlayan bir itici sistemi vardır.[5]
Mengene Ünitesi
Mengene ünitesi, makineye bağlanan kalıbın açılıp kapanmasını ve çapak oluşumunu engellemek için yüksek basınç yaratmakla görevlidir. Makinelerde 3 farklı mengene sistemi kullanılmaktadır.Bunlar;
1. Mekanik sistem;
Bu sistemle mengene aralığı ayarlanabilir kollar ile kontrol edilir ve mekanik sistemin kinematiği ile hareket sağlanır.
2. Hidrolik Sistem;
Hidrolik kapatma sistemlerinde kalıbı açıp kapatma işlemi ve enjeksiyon basıncına karşı gerekli kapatma kuvveti hidrolik silindir ile sağlanır.
3. Hidro-mekanik Sistem ;
Hidro-mekanik kapatma sisteminde kapama işlemi hidrolik silindirler, kilitleme ise özel mekanik elemanlarla sağlanır.[1]
Kontrol Ünitesi
Plastik enjeksiyon prosesinde istenilen tüm değerleri ayarlayan sistemlerdir. Kullanılan enjeksiyon makinelerinde PLC kontrol üniteleri bulunmaktadır. PLC (Programlanabilir Mantıksal Denetleyici), fabrikalardaki üretim bölümlerinde veya makinelerin kontrolü gibi işlemlerin denetiminde kullanılan otomasyon cihazıdır. Bu cihaz, giriş bilgilerini gözle görülmeyecek hızlarla tarayarak buna uygun çıkış bilgilerini gerçek zamana yakın, cevap verecek şekilde çalışır. PLC, kısa sürede daha çok ve kaliteli ürün üretme, çok düşük hata oranlarına sahip üretim yapma gibi unsurların ön plana çıkmasında büyük rol oynar.[6]
Aşamalar
Basit olarak incelendiğinde bir plastik enjeksiyon parçasının imalat süreci şu aşamalardan oluşur:
Plastikleştirme
Çevrimin ilk adımı olan plastikleştirme, granül ya da toz halindeki ham maddenin huniye konması ile başlar. Huniden sonsuz vidaya aktarılan ham madde, vidanın dönme sırasında sürtünme ile açığa çıkan sıcaklık ve vidada bulunan ısıtıcılar ile erimeye başlar. Eriyen hammadde vida boşluğuna ulaşır, hammadde kalıba iletilmek için hazır hale gelir. Plastikleştirme aşaması, vida boşluğunda biriken plastiğin vidayı geriye itmesi sonucunda geri itilme otomatik olarak durmasıyla ve böylece silindire alınan malzeme miktarıyla ayarlanmasıyla tamamlanır.[1]
Kalıbın Kapanması
Enjeksiyon makinesinde bulunan mengene ünitesi tarafından gerçekleştirilen bu aşamada kalıbın iki plakası (erkek ve dişi) birbiri üzerine kapanır. Böylece kalıp boşluğu oluşur ve uygulanan yüksek basınç ve hızlara karşı kalıbın açılmasına engel olur.[1]
Enjeksiyon
Enjeksiyon aşaması esnasında, eriyik hale gelen plastik malzeme, makinenin ucundaki bir meme vasıtası ile kalıbın içine gönderilir. Bu işlem esnasındaki basınç ve hız hidrolik motor ile kontrol edilir. Kalıp boşluğuna iletilen hammadde bu basınç yardımıyla kalıpta sıkışır ve kalıbın sıcaklığına göre daha sıcak olan hammadde soğumaya başlar.[1]
Ütüleme
Parçanın istenen ölçülerde olması ve görünümünde çeşitli hatalar (çöküntü, yamulma, eğilme, vs.) olmaması için bu işlem uygulanır. Basıncın en yüksek olduğu aşamadır. Bu aşamada kalıp içine enjekte edilmiş olan plastik eriyiğin, basınç uygulanarak kalıp boşluğunu iyice doldurması sağlanır. Plastik, kalıp içinde katı hale gelinceye kadar işlem devam eder. Kullanılan hammaddenin özelliğine, parça ebatlarına ve ağırlığına bağlı olarak işlemin süresi değişkenlik gösterir.
Soğutma
Enjekte edilen eriyik hammaddenin, kalıbın içinde sertleşmesine neden olur. Kalıp içinde sertleşen plastik aksesuar kalıptan çıkarılarak endüstrinin hemen her alanında kullanılabilir. Kalıbın soğutulması genellikle kalıp içindeki su kanalları vasıtasıyla yapılır.
Kalıbın Açılması
Kapama ünitesi kalıbın iki tarafı ayrılacak şekilde açılır.
Parçanın kalıptan çıkarılması
Soğuyan parça kalıp açıldığında kalıbın hareketli tarafında kalır ve kalıp tipine göre buradaki maçalar veya iticiler vasıtası ile bitmiş ürün kalıbın hareketli tarafından çıkarılır.

Kaynakça
- ^ a b c d e Pınar, E. 2010. Plastik Enjeksiyon Yöntemiyle İmalatta Hataların Tespiti ve Proses Şartlarının Optimizasyon Uygulaması,Yüksek Lisans Tezi, İstanbul Teknik Üniversitesi Fen Bilimleri Enstitüsü Makine Mühendisliği Anabilim Dalı, İstanbul.
- ^ U.S. patent #133229, dated 19 November 1872.
- ^ Meade, Richard Kidder; McCormack, Harry; Clark, Laurance T.; Sclater, Alexander G.; Lamborn, Lloyd (27 April 2018). "Chemical Age". McCready Publishing Company. Retrieved 27 April 2018 – via Google Books.
- ^ "Köse, E. 2006. Plastik Enjeksiyonda Proses Ve Kalıp Kaynaklı Sorunların Giderilmesi,Yüksek Lisans Tezi, İstanbul Teknik Üniversitesi Fen Bilimleri Enstitüsü Makine Mühendisliği Anabilim Dalı, İstanbul" (PDF). 9 Temmuz 2020 tarihinde kaynağından arşivlendi (PDF). Erişim tarihi: 30 Aralık 2020.
- ^ Kafalı, M. S. 2011. Bilgisayar Destekli Plastik Enjeksiyon Kalıp Tasarımı,Yüksek Lisans Tezi, Erciyes Üniversitesi Fen Bilimleri Enstitüsü Makine Mühendisliği Anabilim Dalı, Kayseri.
- ^ "PLC Nedir? Ne İşe Yarar?". 30 Aralık 2020. 20 Şubat 2015 tarihinde kaynağından arşivlendi. Erişim tarihi: 30 Aralık 2020.