Kimyasal tesisi
Kimyasal tesisi, genellikle büyük ölçekte kimyasallar üreten bir endüstriyel proses tesisidir.[1] Bir kimyasal tesisinin genel amacı, maddelerin kimyasal veya biyolojik dönüşümü ve birbirlerinden ayrılması yoluyla maddi zenginlik yaratmaktır.[2] Kimyasal tesisleri üretim sürecinde özel ekipmanlar, üniteler ve teknolojiler kullanırlar. Polimer, ilaç, gıda, bazı içecek üretim tesisleri, enerji santralleri, petrol rafinerileri veya diğer rafineri çeşitleri, doğal gaz işleme ve biyokimya tesisleri, su ve atık su arıtım tesisleri, kirlilik kontrol ekipmanları gibi diğer tesis çeşitlerinin hepsi, akışkan sistemleri ve kimyasal reaktör sistemleri gibi kimyasal tesis teknolojilerine benzer teknolojiler kullanmaktadır. Bazı kaynaklar bir petrol rafinerisinin, bir ilaç veya bir polimer üreticisinin de bir kimyasal tesisi olarak kabul etmektedir.
Petrokimya tesisleri (petrolü veya petrolden elde edilen türevleri ham madde olarak kullanan tesisler) rafinerilerden aldıkları ürünlerin nakliye maliyetlerini en aza indirmek amacıyla genelde rafinerilerin hemen bitişiğine kurulur. Özel kimyasal[3] ve ince kimyasal üreten tesisler genelde boyut olarak çok daha küçüktür ve kurulacakları konumdan ekonomik olarak fazla etkilenmezler. Temel proje maliyetlerini bir coğrafi konumdan bir diğerine dönüştürmek için çeşitli birçok araç geliştirilmiştir.[4]
Kimyasal prosesler
Kimyasal tesisleri, kimyasal ham maddeleri ürünlere dönüştürmek için ayrıntılı ve endüstriyel ölçekteki yöntemler olan kimyasal prosesleri kullanır. Bir kimyasal proses, üretim kapasiteleri farklı olacak şekilde birden fazla tesiste kullanılabilir. Ayrıca bir kimyasal tesisi, birden fazla ürün üretebilmek için yine birden fazla kimyasal prosesi kullanacak şekilde inşa edilebilir.
Bu başlık kimya mühendisliğine ait serinin bir parçasıdır. |
Kimya mühendisliği |
---|
![]() |
Temel ilkeler |
Ünite prosesleri |
|
Bakış açıları |
|
Bir kimyasal tesisinde ünite veya hat adı verilen büyük tanklar ve bölümler bulunur. Üniteler birbirlerine materyal akışı sağlayabilen borular ve materyali hareket ettirebilecek çeşitli ekipmanlar ile bağlıdır. Söz konusu materyal akımları akışkanlar (boru hatlarıyla taşınan gazlar ve sıvılar) ve bazen de katılar veya sulu karışımlardan oluşur. Bir kimyasal prosesin tümü genellikle ayrı ünitelerde gerçekleşen ve ünite operasyonları adı verilen adımlardan oluşur. Bir ürüne dönüştürülmesi için bir kimyasal prosese veya kimyasal tesise giren ham maddelere genellikle ham madde beslemesi veya kısaca besleme adı verilir. Bütün tesisin işleyeceği ham madde beslemelerine ek olarak, tek bir ünitede işlenecek giriş akımı veya materyal de o ünite için besleme olarak değerlendirilebilir. Tesisin tümünden en son çıkan akımlar nihai ürün ve her bir üniteden çıkan akımlar da ara ürün olarak düşünülebilir. Bununla beraber, bir tesiste elde edilen nihai ürünler, başka bir tesisin ham maddesi olabilir. Örneğin, bir petrol rafinerisinden elde edilen ürünler petrokimya tesislerinde ham madde olarak kullanılabilir ve petrokimya tesislerinden elde edilen ürünler de ilaç fabrikaları için birer ham madde olabilir.
Ham maddeler ve ürünler, tek başına birer bileşik veya karışım olabilirler. Karışımlardaki bileşenleri tamamen birbirinden ayırmak genelde zahmete değer bir işlem değildir, bu sebeple ürünün saflık seviyesi ürün gereksinimlerine ve proses ekonomisine göre belirlenir.
Operasyonlar
Kimyasal prosesler sürekli veya kesikli operasyonlarla gerçekleştirilebilirler.
Kesikli operasyon
Kesikli operasyonda üretim zamansal olarak sıralanmış partilerle gerçekleşir. Bir ham madde partisi öncelikle proses ünitesine beslenir (veya boşaltılır). Kimyasal proses ünitede gerçekleştirildikten sonra da elde edilen ürün veya ürünler üniteden alınır. Bu tür kesikli üretimler her yeni gelen ham madde partisiyle tekrar tekrar gerçekleştirilebilir. Kesikli operasyon, esnekliği kadar kolay izlenebildiğinden dolayı ilaç ve özel kimyasallar üretiminde sıklıkla kullanılan bir yöntemdir. Kesikli üretim tesisleri özel kimyasalların, ince kimyasalların ve ilaç etken maddelerinin (API) üretiminde daha yaygınken, sürekli üretim yapan tesisler genelde ticari kimyasalların veya petrokimyasalların üretiminde kullanılır.
Sürekli operasyon
Sürekli operasyonda tüm üretim adımları zaman içinde sürekli olarak devam etmektedir. Normal bir sürekli operasyonda devamlı hareket halindeki materyaller olan besleme ve ürün akışları ile üretim prosesinin kendisi de aynı anda sürekli gerçekleşir. Sürekli operasyon gerçekleştiren kimyasal tesisleri ve üniteler genellikle ya yatışkın hâldedir ya da yatışkın hâle yakın çalışır. Yatışkın hâl, prosesle alakalı değerlerin zamanla değişmediği, operasyon boyunca sabit kaldığı anlamına gelmektedir. Bu sabit değerler akış debileri, ısıtma veya soğutma hızları, sıcaklıklar, basınçlar ve herhangi bir noktadaki kimyasal bileşim gibi niceliklerdir. Petrol rafinerileri gibi birçok büyük ölçekli işletmede sürekli operasyon daha verimli bir işlemdir. Kimyasal tesislerindeki bazı üniteler sürekli çalışırken bazılarının da kesikli çalışabilmesi mümkündür. Örnek olarak sürekli distilasyon ve kesikli distilasyona bakılabilir. Bir tesis veya bir ünitenin birim zamanda ürettiği ürün veya işleyebildiği ham madde miktarına söz konusu tesis veya ünitenin kapasitesi adı verilir. Örneğin bir petrol rafinerisinin kapasitesi günde arıtılan ham petrol varili cinsinden verilebilir; bir kimyasal tesisinin kapasitesi de günde üretilen ürünün tonu cinsinden verilebilir. Gerçekte bir tesis (veya bir ünite) günlük işletiminde tam kapasitesinin belli bir yüzdesinde çalışır. Mühendisler ağırlıklı olarak akışkanlarla çalışan tesisler için genelde %90, ağırlıklı olarak katılarla çalışan tesisler için de genelde %80 çalışma kapasitesi kabulü yapmaktadırlar.
Üniteler ve akışkan sistemleri
Belli ünite operasyonları, yine belli ünitelerde gerçekleştirilir. Bazı üniteler ortam sıcaklığı ve basıncında çalışsalar da, birçok ünite daha yüksek veya alçak sıcaklık ve basınçlarda çalışmaktadır. Kimyasal tesislerindeki tanklar genellikle yüksek basınç veya vakuma dayanıklı, yuvarlatılmış uçlara sahip silindirlerdir. Kimyasal reaktörlerde gerçekleşen reaksiyonlar yoluyla belli bileşikler başka bileşiklere çevrilebilirler. Kimyasal reaktörler reaksiyona girecek akışkanların üzerinden akacağı katı heterojen katalizörlere sahip dolgulu yataklar olabileceği gibi, reaksiyonların gerçekleştiği basit karıştırmalı tanklar biçiminde de olabilirler. Katı heterojen katalizörler bazen kok gibi tortul maddelerden dolayı "zehirlenebildiklerinden" yenilenmeleri gerekli olabilir. İyi bir karıştırma sağlamak için bazı durumlarda akışkan yataklar da kullanılabilir. Ayrıca çözdürme de dahil olmak üzere karıştırma, ayırma, ısıtma, soğutma veya bu sayılan süreçlerin çeşitli şekillerde birleştirildiği üniteler de kimyasal tesislerinde bulunabilir. Örneğin kimyasal reaktörler genellikle içindeki sıvıları karıştırmak için karıştırıcı sistemlere, karışım sıcaklığını belli bir noktada tutabilmek için de ısıtma ve soğutma sistemlerine sahiptir. Tesisler büyük ölçekte tasarlanırken, kimyasal reaksiyonlarla üretilen veya absorbe edilen ısı dikkate alınmalıdır. Bazı tesislerde fermantasyon veya enzim üretimi gibi biyokimyasal işlemler için canlı (çoğunlukla bakteri) kültürlerine sahip üniteler bulunabilir.
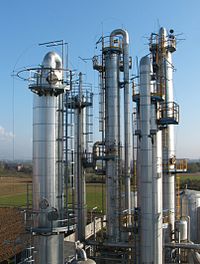
Filtrasyon, çöktürme, ekstraksiyon (özütleme veya liçing olarak da adlandırılır), distilasyon, rekristalizasyon (yeniden kristallendirme), ters osmoz, kurutma, absorpsiyon ve adsorpsiyon gibi ayırma işlemleri kimyasal tesislerinde kullanılan çeşitli yöntemlerdir. Isı değiştiriciler kaynatma ve yoğuşturma işlemlerinin yanı sıra, ısıtma ve soğutma işlemleri için kullanılır. Çoğu zaman distilasyon kuleleri gibi ünitelere bağlı bir şekilde kullanılırlar. Ham maddeleri, ara ürünleri, nihai ürünleri ve atıkları depolamak için kullanılan depolama tankları da tesiste mevcut olabilir. Depolama tanklarında genellikle ne kadar dolu olduklarını gösteren bir seviye göstergesi bulunur. Bazı durumlarda oldukça büyük üniteleri ve ilgili ekipmanları taşıyan veya destekleyen yapılar bulunur. Çalışanların denetleme ve bakım yapabilmeleri, numune alabilmeleri için ünitelerde merdivenler, katlar ve çeşitli basamaklar bulunur. Özellikle petrol terminallerinde çok sayıda depolama tankı bulunduran bir tesis veya fabrika sahası, tank çiftliği olarak adlandırılabilir.
Çeşitli çaplarda boru hatları, akışı kontrol etmek veya durdurmak için çeşitli vana tipleri, sıvıları hareket ettirmek veya basıncını artırmak için pompalar ve yine gazları hareket ettirmek ve basıncını artırmak için kompresörler, sıvı ve gazları tesis boyunca taşımak için kullanılan akışkan sistemleridir. Tanklar, boru hatları, yüksek veya çok düşük sıcaklıklarda çalışan diğer ekipmanlar, genellikle çalışanların güvenliğini sağlamak ve ekipman içindeki sıcaklığı korumak için yalıtım malzemeleriyle kaplanabilir. Bir tesisteki üniteler ve akışkan sistemlerinde belirli konumlarda sıcaklık ölçerler, basınç sensörleri ve akış ölçüm cihazları gibi ölçüm aletleri vardır. Kimyasal veya fiziksel özelliklerin analizi için çevrimiçi analiz ediciler günümüzde daha yaygın hale gelmiştir. Reaktanların veya tesiste ekstrakte edilen katı maddelerin çözdürülmesinde, kimyasal reaksiyonlar için uygun sıvı ortamın sağlanması veya katıların çözünmesini sağlanarak sıvılaştırılmalarında çözücüler kullanılabilir.
Kimyasal tesisi tasarımı

Günümüzde kimyasal tesislerin tasarımı kimya mühendisleri tarafından yapılmaktadır. Tarihsel olarak bu durum her zaman bu şekilde olmamakla beraber kimya mühendisliği bir disiplin olarak kurulmadan önce birçok kimyasal tesisi gelişigüzel bir şekilde inşa edilmiştir. Kimya mühendisliği ilk kez 1887 yılında, Manchester Üniversitesi'nde George E. Davis tarafından endüstriyel kimya uygulamalarının çeşitli yönlerini kapsayan ve on iki dersten oluşan kimya mühendisliği kursunun verilmesi ile bir meslek olarak kurulmuştur.[5] Bunun sonucu olarak George E. Davis günümüzde dünyanın ilk kimya mühendisi olarak kabul edilmektedir. Günümüzde de kimya mühendisliği bir meslektir ve tecrübeli kimya mühendisleri Kimya Mühendisleri Enstitüsü aracılığıyla "yetkili" mühendis statüsü kazanabilmektedirler. Türkiye'de 6235 Sayılı Türk Mühendis ve Mimar Odaları Birliği Kanunu'nun 33. maddesi gereğince Türkiye'de mühendislik ve mimarlık mesleklerini icra etmek isteyen her kişi uygun bir odaya kaydolmak ve üyeliğini korumak zorundadır.[6] Buna bağlı olarak kimya mühendisleri Türkiye'de Kimya Mühendisleri Odası'na üye olup odanın sağladığı çeşitli imkânlardan faydalanabilirler.
Tesis tasarımında yeni tasarım fikirlerinin ortalama olarak yalnızca yüzde 1'inden azı ticari hâle gelir. Maliyet çalışmaları tasarım sürecinde kârlı olmayacak tasarımların elenmesinde kullanılan bir ön inceleme yöntemidir. Bir prosesin kârlı olduğu ortadaysa, güvenlik, çevresel kısıtlamalar, kontrol edilebilirlik vb. diğer faktörler göz önünde bulundurulur.[2] Tesis tasarımındaki genel amaç, istenen kısıtlamalar dahilinde “optimum tasarımlar” oluşturmak veya sentezlemektir.[7]
Çoğu zaman kimyagerler laboratuvarda kimyasal reaksiyonları veya diğer kimyasal ilkeleri, genellikle “kesikli tipte”, küçük ölçekli deneylerle araştırırlar. Elde edilen bu kimyasal bilgiler kimya mühendisleri tarafından kendi uzmanlıklarıyla kimyasal bir proses oluşturmak ve laboratuvardaki kesikli işlemin boyutunu veya kapasitesini artırmak için kullanılır. Genellikle büyük bir tesisin inşasından önce çeşitli tasarım ve işletme bilgileri edinmek için pilot tesis adı verilen küçük bir kimyasal tesis inşa edilir. Pilot tesisten elde edilen veriler ve işletme deneyimi ile daha yüksek veya tam kapasitede çalışmak için büyük ölçekli bir tesisin tasarımına girişilebilir. Bir tesis tasarımının temel yönleri belirlendikten sonra makine ve elektrik mühendisleri tesisin mekanik ve elektrik ile ilgili detaylarıyla ilgilenebilirler. İnşaat mühendisleri, tesisteki yapıların üniteleri, boru hatlarını ve diğer ekipmanların ağırlığını taşıyabilmesini sağlamak için tesis tasarımına dahil olabilirler.
Kimyasal tesislerin veya proseslerin üniteleri, akımları ve akışkan sistemleri çok basitleştirilmiş diyagramlar olan blok akış şemaları veya daha ayrıntılı olan proses akış şemaları ile gösterilebilir. Akımlar ve diğer boru hatları, ok başlarının akış yönünü gösterdiği çizgilerle gösterilir. Blok şemalarda, birimler genellikle basit dörtgen bloklar ile gösterilir. Proses akış şemaları ise daha detaylı semboller kullanır ve pompaları, kompresörleri ve ana vanaları da gösterebilir. Çeşitli akımlar için akış debilerinin muhtemel değerleri veya aralıkları, istenen tesis kapasitesine göre gerekli kütle dengelerinin kurulup hesaplanmasıyla belirlenir. Çeşitli yerlerde ihtiyaç duyulan ısıtma ve soğutma miktarlarını hesaplamak ve ısı değiştiricilerini boyutlandırmak için reaksiyon ısılarının, ısı kapasitelerinin, beklenen sıcaklıkların ve çeşitli noktalardaki basınçların esas alınmasıyla da enerji dengeleri kurulur. Kimyasal tesisinin tasarımı, tüm boru tesisatını, vanaları ve ölçüm cihazlarını özel sembollerle gösteren bir borulandırma ve enstrümantasyon şemasında (P&ID) daha ayrıntılı olarak gösterilebilir. Bir tesisin tamamının bir borulandırma ve enstrümantasyon şemasında gösterilmesi genellikle zor ve karmaşıktır, bu nedenle çoğu zaman sadece tek bir ünite veya akış sistemi bu şema çeşidi ile gösterilir.

Tesis tasarımında ünitelerin her biri sahip olmaları gereken maksimum kapasite için boyutlandırılır. Benzer şekilde borular, pompalar, kompresörler ve ilgili ekipmanların boyutları, sağlamakta zorunlu oldukları akış kapasitelerine göre seçilir. Elektrik ve su temini gibi servis akımları da tesis tasarımına dahil edilmelidir. Tesisin veya ünitenin başlatılması ve kapatılması gibi rutin veya alternatif işletme prosedürleri için de tesise ek boru hatlarının dahil edilmesi gerekebilir. Akışkan sistemlerinin tasarımında genellikle bir tesisin çeşitli ünitelerinin veya bölümlerinin etrafına izolasyon vanaları kullanılır. Böylece bir ünitede sızıntı gibi bir sorun olması durumunda tesisin istenilen kısmı izole edilebilir. Pnömatik veya hidrolik olarak çalıştırılan vanalar kullanıldığında sürücü sistemlere bir basınç hatlarının eklenmesi gereklidir. Tesis boyunca numune alınması gereken noktalardaki vanalar ve numune alma hatları ayrıntılı tasarıma dahil edilmelidir. Gerektiği durumlarda numune alma hattının basıncını ve sıcaklığını düşürecek basınç düşürme vanası ve numune soğutucu gibi ekipmanlar konulmalıdır.
Tesisteki tüm tanklar, borular hatları, vanalar, pompalar, kompresörler ve diğer tüm ünite ve akışkan sistemleri, karşılaşabilecekleri bütün sıcaklık, basınç ve diğer koşullara dayanabilecek şekilde derecelendirilmeli veya tasarlanmalıdır. Buna uygun tüm güvenlik faktörleri de bu duruma dahildir. Tüm bu üniteler ve ekipmanlar, temas edecekleri kimyasallara uzun süre maruz kalmaya dayanabilmelerini sağlamak için malzeme uyumluluğu açısından da kontrol edilmelidir. Isıtma, ekzotermik reaksiyonlar veya bazı pompalar ve kompresörler gibi derecelendirmesinin muhtemelen ötesinde bir basınçla çalışacak kapalı sistemlerde, güvenliği sağlamak ve aşırı basınç oluşmasını önlemek için uygun boyutta bir basınç tahliye vanası bulunmalıdır. Genelde bu parametrelerin tümü (sıcaklıklar, basınçlar, akış vb.) tesisin bilinen bir ciddi tehlike riski içermemesinden emin olmak amacıyla, Hazop veya hata ağacı analizi ile birlikte kapsamlı bir şekilde analiz edilir.
Tesisin tabi olduğu tüm kısıtlamalar dahilinde, tasarım parametreleri, bir yandan çalışanların ve etraftaki halkın güvenliği ve refahını sağlarken bir yandan da iyi bir ekonomik performans göstermek için optimize edilir. Bir tesis, ham madde veya ekonomik koşulların değişebileceği ve yeniden optimizasyonun gerekli olabileceği durumlar göz önünde bulundurularak esnekliği sağlamak için uygun tasarım parametreleri aralığında çalışacak şekilde tasarlanabilir. Günümüzde kimyasal tesisi tasarımı ve optimizasyonuna yardımcı olmak için bilgisayar simülasyonları veya diğer benzeri bilgisayar hesaplamaları kullanılmaktadır.
Tesis işletimi
Proses kontrol
Proses kontrolünde, çeşitli sensörlerden veya tesisteki diğer cihazlardan otomatik olarak toplanan veriler, tesisi çalıştırmak için çeşitli ekipmanların kontrolü ve böylece tesisin tümünün çalışmasını kontrol etmek için kullanılır. Bu fonksiyonu otomatik bir şekilde gerçekleştirmek için veri sinyalleri toplayan ve kontrol sinyalleri gönderen cihazlar proses kontrol edicileridir. Bundan önce ara sıra pnömatik kontrol ediciler kullanılmaktaydı. Şimdiyse elektrikli kontrol ediciler daha yaygındır. Bir tesiste genellikle önemli sıcaklıkların, basınçların, sıvı akış hızları ve seviyelerinin, ana vanaların, pompaların ve diğer ekipmanların çalışma koşulları gibi parametrelerin görüntülendiği bir kontrol odası bulunur. Buna ek olarak, kontrol odasında bulunan operatörler otomatik kontrol sistemini geçersiz kılabilir ve tesis işletiminin çeşitli unsurlarını kontrol edebilirler. Bilgisayarla yapılan proses kontrol daha modern bir teknolojidir. Ham madde bileşiminde, ürün gereksinimlerinde, ekonomide ve diğer kısıtlamalardaki olası değişimlere dayanarak, tesisin çalışma koşulları kârı en üst düzeye çıkarmak için proses kontrol ile yeniden optimize edilebilir.
Çalışanlar
Bütün endüstriyel alanlarda olduğu gibi, bir kimyasal tesisinde de genellikle departmanlara, bölümlere veya diğer çalışma gruplarına ayrılmış çeşitli yetkinliklerde çalışanlar vardır. Bu çalışanlar arasında mühendisler, tesis operatörleri ve bakım teknisyenleri vardır. Sahada kimyagerler, yönetim/idare ve ofis çalışanları da bulunabilir. İşletme veya bakımla ilgilenen mühendisler arasında kimya mühendisleri, mekanik ekipmanların bakımı için makine mühendisleri, elektrikli ekipmanlar ve bilgisayar ekipmanları için de elektrik ve bilgisayar mühendisleri vardır.
Taşıma
Büyük miktarlarda sıvı ham madde veya ürün, bir tesise boru hatları, demiryolu tankerleri veya tanker kamyonlarıyla girebilir veya çıkabilir. Örneğin, ham petrol genellikle tankerler ve boru hatları ile rafineriye gelir. Boru hatları aynı zamanda rafineride üretilen petrokimyasalları yakındaki bir petrokimya tesisine taşıyabilir. Doğal gaz, doğal gaz işleme tesislerinden, nihai tüketiciye kadar boru hatları ile taşınan bir üründür. Büyük miktarlardaki sıvı ham maddeler proses ünitelerine pompalanarak ulaştırılır. Daha küçük miktarlardaki ham madde veya ürünler varillerle tesislere sevk edilebilir. Kimyasalların endüstriyel miktarlarda paketlenmesi ve taşınması için yaklaşık 55 galonluk (208.2 litre) varil kullanımı yaygındır. Daha küçük ham madde beslemeleri, proses ünitelerine işçiler tarafından varillerden veya konteynerlerden eklenebilir.
Bakım
Tesise ham madde beslenmesi, işletilmesi ve ürünün nakliye için paketlenmesi veya hazırlanmasına ek olarak, rutin analizler için numune almak, sorunların giderimi, rutin ve rutin olmayan bakımları gerçekleştirebilmek için tesis çalışanlarına ihtiyaç vardır. Eskimiş katalizörlerin, analiz edici reaktanların, çeşitli sensörlerin ve mekanik parçaların yenilenmesi ile periyodik denetlemeler, rutin bakım kapsamına girer. Rutin olmayan bakımda ise sızdırmalar, ürün özelliklerini sağlanamaması, vanaların, pompaların, kompresörlerin, sensörlerin vb. ekipmanların arızalanması gibi sorunların araştırılması ve çözümlenmesi yer alır.
Yasalara ve mevzuata uygunluk
Kimyasal maddelerle çalışırken kimyasal kazalar gibi sorunlardan kaçınmakta güvenlik önemli bir konudur. ABD'de yasalar, işverenlerin çalışanlarına çalışma gerçekleştirdikleri her tür kimyasal için Malzeme Güvenlik Bilgi Formları (MSDS) sağlamasını zorunlu tutar. Belirli bir kimyasal madde için bir MSDS, kimyasalı satın alan kişiye tedarikçi tarafından sağlanır. ABD'deki Kaynak Korunması ve Geri Kazanımı Yasası (RCRA), Zehirli Madde Kontrol Yasası (TSCA) gibi kanunlar ve Kimyasal Tesisi Terörle Mücadele Standartları gibi kimyasal güvenliği, tehlikeli atık ve kirlilik gibi konuları kapsamına alan diğer yasa ve yönetmelikler incelenmelidir.
Tehlikeli madde ekipleri, kimyasal sızıntılarıyla başa çıkmak için eğitilmişlerdir. Kimyasal tesislerdeki potansiyel tehlikeleri değerlendirmek için Proses Tehlike Analizi (PHA) kullanılır. 1998 yılında ABD Kimyasal Güvenlik ve Tehlike Araştırma Kurulu faaliyete geçti.
Tesis işletmeleri
Bir tesisin fiili üretiminin veya prosesi kapalı alanda, dışarıda veya kısmi olarak hem içeride hem dışarıda gerçekleşebilir. Tesisteki tüm üniteler aşama aşama inşa edilebileceği gibi, modüler proses ünitelerinden de meydana gelebilirler. Büyük modüler ünitelerin imali beceri ve teknik uzmanlık gerektiren bir iştir. Modüler üniteler, geleneksel yolla aşama aşama inşa edilen bir tesis veya ünitenin yapacağı işi gerçekleştirebilmek için gerekli olan tüm ekipmanları içerecek şekilde inşa edilirler. Bununla birlikte, modüler üniteler çelik çerçeve yapılar içine kurulur ve bu sayede sahada tekrar inşa edilmesine gerek kalmadan istenilen bölgeye sevk edilebilir. Modüler proses ünitelerinin sahaya kurulumunda daha az işgücü gerektiğinden dolayı risk ve kaza ihtimali azalır, bu sayede sıfırdan aşama aşama inşa edilecek ünitelere göre daha sağlıklı ve az sorunla çalışır. Bir tesisin fiili üretim kısmı genellikle oldukça endüstriyel bir ortam görünümündedir. Tesislerin hemen hepsinde baretler ve iş ayakkabıları giyilir. Zeminler ve merdivenler genellikle metal ızgaradan yapılır ve neredeyse hiçbir dekorasyon bulundurmazlar. Tesislerde kirlilik kontrol veya atık arıtım işletmeleri ve ekipmanları bulunabilir. Bazen mevcut tesisler değişen ekonomi, ham madde veya ürün ihtiyaçlarına göre genişletilebilir veya değiştirilebilir. Diğer üretim tesislerinde olduğu gibi, kimyasal tesislerinde de nakliye, mal kabul ve depolama işletmeleri bulunabilir. Tüm bunlara ek olarak, sahadaki üretimi desteklemek için genellikle kapalı alanlarda faaliyet göstere başka işletmeler de bulunabilir.
Bazı basit numune analizleri tesis sahasındaki operatörler tarafından yapılabilse de, genelde kimyasal tesislerinde kimyagerlerin fabrikadan alınan örnekleri analiz ettiği bir laboratuvar bulunur. Laboratuvarlarda kimyasalların analizi veya fiziksel özelliklerin belirlenmesi gibi analizler gerçekleştirilmektedir. Kalite şartlarının sağlandığından emin olmak için tesise gelen ham maddeler, ara ürünler ve nihai ürünler üzerinde gerçekleştirilen rutin kalite kontrol işlemleri, söz konusu numune analizleri kapsamındadır. Rutin olmayan numuneler de tesisin proses problemlerinin araştırılması için alınıp analiz edilebilir. Daha büyük kimya şirketlerinin genellikle pilot tesisleri olan, ürün ve üretim süreçlerini geliştirmek ve test etmek için sahip oldukları araştırma laboratuvarları vardır. Ancak söz konusu araştırma laboratuvarları üretim tesislerinden ayrı bir yerde bulunabilir.
Bir tesiste onarım veya bakım ekipmanlarının bulunduğu bir atölye veya bakım tesisi bulunabilir. Ayrıca genelde mühendisler, yönetim veya idare ve ziyaretçi kabulü için de bazı ofis alanları da bulunur. Bu alanlardaki dekorasyon bilinen ofis ortamına çok daha yakındır.
Ticari kimyasal tesislerinin organizasyonu
Özellikle ticari kimyasal ve petrokimyasal üretimi için kullanılan kimyasal tesisleri altyapı ihtiyaçları nedeniyle dünyada nispeten az sayıda üretim yerinde bulunmaktadır. Tesisin konumununun önemi, daha önce de bahsedildiği üzere kesikli üretim yapan özel kimyasal veya ince kimyasal tesisleri için daha azdır. Tüm ticari kimyasal ve petrokimyasal üreten tesisler aynı noktada üretim yapmamakla beraber birbirleriyle alakalı materyalleri üreten tesisler malzeme, enerji, servis akımı (su, elektrik) verimliliğini ve diğer ölçek ekonomilerini teşvik etmek için çoğunlukla aynı konumda bulunurlar. Bu üretim yerlerinde genellikle enerji santralleri, liman işletmeleri, karayolu ve demiryolu terminalleri gibi büyük ölçekli altyapıları paylaşan organize hâlde birçok kimyasal tesis bulunabilir. Örneğin Birleşik Krallık'ta, Kuzeybatı İngiltere'deki Mersey Nehri yakınında, Yorkshire'ın doğu kıyısındaki Humber'da, İskoçya'da, Firth of Forth yakınındaki Grangemouth'ta ve Kuzeydoğu İngiltere Organize Proses Endüstrisi'nin (NEPIC) bir parçası olan Teesside'da bulunan dört ana ticari kimyasal üretimi bölgesi bulunmaktadır.[8] İngiltere'nin petrokimyasallarının yaklaşık %50'si Tees Nehri ağzında bulunan Teesside bölgesindeki üç büyük kimya parkı Wilton,[9] Billingham ve Seal Sands'te üretilir.
Korozyon ve yeni malzemelerin kullanımı
Kimyasal proses tesislerinde korozyon yılda milyarlarca dolar harcamaya sebep olan önemli bir sorundur. Metallerin elektrokimyasal korozyonu, asit buharları ve diğer elektrolitik etkileşimler nedeniyle kimyasal proses tesislerinde göze çarpan bir durumdur. Son zamanlarda inşaat malzemesi olarak FRP (lif takviyeli plastik) kullanılmaktadır. İngiliz BS4994 standardı, kazanlar, tanklar vb. ekipmanların tasarımı ve inşası için yaygın olarak kullanılmaktadır.
Ayrıca bakınız
- BS4994
- İnce kimyasallar
- Kimya endüstrisi
- Kimya Mühendisleri Enstitüsü (IChemE)
- Kimyasal kaza
- Kimyasal proses modelleme
- Kimyasal tesisi maliyet endeksleri
- Kuzeydoğu İngiltere Organize Proses Endüstrisi
- Lifli polimer tanklar
- Özel kimyasallar
- Petrokimya endüstrisinde enstrümantasyon
- Petrokimyasallar
- S grafiği
- Ünite operasyonları
Kaynakça
- ^ Chemical Plant Technology: An Introductory Manual. Longmans. 1970.
- ^ a b Conceptual Design of Chemical Processes. McGraw-Hill. 1988. ISBN 978-0-07-017762-8.
- ^ Stork (2004). "Speciality Chemicals" (PDF). Chemical & Engineering News supplement 82. ss. 35-39. 8 Ekim 2008 tarihinde kaynağından arşivlendi (PDF). Erişim tarihi: 22 Haziran 2020.
- ^ "Plant Construction Location Factor - Intratec Knowledge Base". 6 Mart 2014 tarihinde kaynağından arşivlendi. Erişim tarihi: 22 Haziran 2020.
- ^ "Seventy Five Years of Chemical Engineering". Purdue University. 18 Mayıs 2011 tarihinde kaynağından arşivlendi. Erişim tarihi: 13 Ağustos 2013.
- ^ "6235 Sayılı Türk Mühendis ve Mimar Odaları Birliği Kanunu". Türk Mühendis ve Mimar Odaları Birliği. 2020. 13 Şubat 2015 tarihinde kaynağından arşivlendi. Erişim tarihi: 5 Temmuz 2020.
- ^ Chemical product design. Cambridge University Press. 2001.
- ^ "Chemicals–the UK advantage" (PDF). s. 9–10. 29 Ekim 2013 tarihinde kaynağından (PDF) arşivlendi. Erişim tarihi: 10 Temmuz 2013.
- ^ Wilton the First Fifty Years. Falcon Press. 1999. ISBN 978-1872339016.
Konuyla ilgili yayınlar
- ASME B73 Standards Committee, Chemical Standard Pumps 7 Ağustos 2020 tarihinde Wayback Machine sitesinde arşivlendi.
- Process plant design : project management from inquiry to acceptance. Weinheim: Wiley-VCH. 2008. ISBN 978-3527313136.
- Process plants : a handbook for inherently safer design. 2nd. Boca Raton, FL: CRC Press/Taylor & Francis. 2010. ISBN 978-1439804551.
- Chemical engineering design: principles, practice and economics of plant and process design. 2nd. Oxford: Butterworth-Heinemann. 2013. ISBN 9780080966595.
- Process development : from the initial idea to the chemical production plant. 1st ed., repr. Weinheim: Wiley-VCH. 2005. ISBN 978-3527310890.
- Plant design and economics for chemical engineers. 5th. New York: McGraw-Hill. 2003. ISBN 978-0072392661.
- Chemical Plant