Kamçı etkisi

Kamçı etkisi (İngilizce: Bullwhip effect), tedarik zincirinde tahminlerin verimsizliğini tarif eden bir dağıtım kanalı olgusudur. Tedarik zincirinde, müşteri ihtiyaçlarının maksimum seviyelere ulaştığı durumların envanterde yaratacağı büyük dalgalanmaları ifade eder. Bu kavram ilk olarak Jay Forrester ‘ın Industrial Dynamics (1961) kitabında ortaya atılmıştır, bu sebeple Forrester etkisi olarak da bilinir. Kamçı etkisi ismiyle anılmasının sebebi, kamçının salınım sırasında genliğinin artarak devam etmesidir. Dalga kaynağından uzaklaştıkça, dalga desenindeki sapmalar artmaktadır. Benzer şekilde, yapılan tahminlerin doğruluğu tedarik zincirinde yukarılara çıkıldıkça azalır. Örneğin perakende sektöründe, birçok tüketici ürününde tüketim miktarları oldukça tutarlıdır. Ancak bu sinyal, tüketici satın alma alışkanlıklarından uzaklaştıkça daha kaotik ve beklenmedik hale gelebilir.
1990 da, Standford Üniversitesinden Mühendislik ve Yönetim bilimleri profesörü Hau Lee'nin, Volvo hakkında yazdığı bir hikâye, kavramın tedarik zinciriyle bütünleşmesine yardım etmiştir. Satış ve pazarlama,yeşil arabalardaki fazlalığı yok etmek için bir program geliştirerek aşırı stokları ortadan kaldırmıştır. Marketin talebi karşılanırken; üretimin, yapılan promosyon planlarından haberi yoktu. Onun yerine üretim, yeşil arabaların market talebindeki artışın göstergesi olarak satışlardaki artışları baz almış, buna istinaden üretim miktarlarını artırmışlardır.[1]
Araştırmalar, taleplerdeki +/- %5 dalgalanmanın, tedarik zincirinde +/- %40 a kadar dalgalanmaya yol açabileceğini göstermiştir. Bir kamçının vuruşundaki gibi, bilekteki ufak bir hareket (satış talebindeki bir kayma) kamçının sonunda büyük bir harekete sebep olur. (üretimin karşılaması).
Nedenler
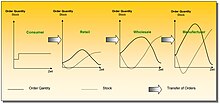
Müşteri talepleri nadiren tam kararlı olduğundan, işletmelerin envanteri ve diğer kaynaklarını doğru konumlandırması için talebi tahmin etmeleri gerekir. Tahminler istatistiklere dayalıdır ve nadiren tam doğruları verir. Tahmin hataları sebebiyle, işletmeler ”güvenlik stoğu ” denilen envanter tamponları bulundururlar.
Tedarik zincirinde, son müşteriden hammadde sağlayıcısına kadar tedarik zincirinin tüm parçaları taleplerde yüksek varyanslar ile karşılaşılar ve bu sebeple emniyet stoklarına ihtiyaç duyarlar. Talebin yükseldiği dönemde, alt kademedeki tedarik zinciri parçaları siparişlerini arttırırlar. Talebin düştüğü veya durduğu dönemlerde de envanteri azaltmamış olurlar. Tedarik zincirinin üst kademelerine çıkıldıkça, bu varyansların etkisi büyür. Bu olaylar dizisi, MIT Sloan School of Management tarafından 1960'lı yıllarda geliştirilen bira dağıtım oyununda (beer game) iyi bir şekilde simüle edilmiştir.
Sebepler ayrıca, davranışsal ve operasyonel olarak birbirinden ayrılabilir.
Davranışsal Sebepler
- Kötü temel stok politikaları
- Geri bildirimlerde ve gecikmelerdeki yanlış algılamalar
- Karşılanamayan siparişlerin ardından acil siparişler
- Diğer oyuncuların makullük sınırlarının değerlendirilip, oluşabilecek risklerin sezilmesi
İnsan faktörünün davranışsal rolünün tedarik zincirine etkisi büyük ölçüde çözülememiştir. Bununla birlikte çalışmalar, tedarik zinciri ortamında güvenliğe önem veren tedbirli insanların, risk alanlara göre daha kötü performans sergilediklerini göstermiştir. Yüksek yeterliliğe sahip kişilerin tedarik zincirinde kamçı etkisiyle karşılaşma tehlikeleri düşüktür.
Operasyonel Sebepler
- Bağımlı talep işlemi
- Tahmin hataları
- Her talep gözleminde envanter kontrol parametrelerinin ayarlanması
- Tedarik süresi değişkenliği (tedarik süresiyle ilgili tahmin hatası)
- Parti büyüklüğü/sipariş senkronizasyonu
- Taleplerin birleştirilmesi
- İşlem güdüsü
- Miktar indirimi
- Ticari promosyonlar ve gelecek alımları
- Kısa kalma öngörüsü
- Tedarikçilerin tahsis kuralı
- Kısa kalma kurgusu
- Envanter ve üretim stratejisinin yalın ve tam zamanında üretimle yönetilmesi
Sonuçlar
Büyük güvenlik stoklarına ek olarak bu etki, verimsiz üretimden veya fazla stoklardan kaynaklı da götürebilir. Bütün üreticiler, tedarik zincirindeki müşterilerinin taleplerinin tam olarak karşılanma gereksinimi duyarlar. Bu da dağıtım kanallarda düşük kullanım oranlarına sebep olur.
Emniyet stoklarına sahip olunmasına rağmen, başarısız müşteri hizmetlerinin sonucu olarak oluşan stoksuz kalma durumları sipariş kaybına neden olabilmektedir. Bunun yanında başarısız müşteri hizmetlerinin, genel imaj ve müşteri sadakati üzerinde ölçülemeyen sonuçları da vardır. Bir işletme gerçekleştiremediği siparişlerden kaynaklanan, sözleşmelerdeki cezalarla başa çıkmak durumundadır. Dahası, talep değişkenliğini yönetmek için tekrarlanan işe alım ve işten çıkarmalar, eğitimler ve kanuni zorunluluklar nedeniyle ekstra maliyetlere de katlanırlar.
Önlemler
Teoride, bütün siparişler her seferinde tam zamanında karşılanırsa kamçı etkisi meydana gelmez. Bu bulgular kamçı etkisini, öngörü odaklı tedarik zinciri içerisinde bir problem olarak kabul eden uzmanların görüşleriyle tutarlıdır. Bu nedenle müşteri taleplerinin görünürlüğünü mümkün olan en uzak noktaya kadar genişletmek gereklidir.
Bu müşteri ihtiyaçlarına tepki veren talep odaklı tedarik zinciri kurmanın bir yoludur. Üretimde bu konsept kanban olarak anılır. Bu model Wall Mart ın dağıtım sisteminde başarılı oldu. Wall mart da ana ofis POS bilgilerini gün içinde birkaç kez alır. Bu talep bilgileri Wall Mart dağıtım merkezlerinin ve bunların tedarikçilerinin transfer kuyruklarında kullanılır. Elde edilen sonuç müşteri ihtiyaçlarının ve tedarik zinciri boyunca envanter hareketlerinin neredeyse mükemmel görünürlüğüdür. Daha iyi bilgi daha iyi envanter pozisyonu almaya ve tedarik zinciri boyunca daha düşük maliyete götürür.
“Toplam Miktar” konsepti kamçı etkisiyle mücadele edebileceğimiz hatta önleyebileceğimiz bir metottur. Bu metot özellikle Alman otomotiv endüstrisinin gelişmiş tedarik zincirlerinde uygulandı ve geliştirilmiştir. Orijinal ekipman üreticisi (OEM) ile tedarikçileri arasında çok çeşitli elektronik data transferi (EDI) formatları kurulmasına yardımcı olmuştur.
Talep odaklı tedarik zincirinin uygulanmasındaki engelleri bilgi teknolojisi yatırımı, esneklik ve müşteri ihtiyaçlarına odaklanman firma kültürünün oluşturulması olarak sıralayabiliriz. Diğer bir ön koşulda bütün tedarik zinciri paydaşlarının tam güvene dayalı işbirliği ve bilgi paylaşımı ile daha çok kazanç elde edeceklerinin farkına varmalarıdır.
Metotlar belirsizliğin, değişkenliğin ve tedarik zamanlarının azaltılması üzerine tasarlanmıştır.: - Satıcı yönetimli envanter (vendor managed inventory)
- Tam zamanında üretim(JIT)
- Talep odaklı MRP
- Stratejik işbirliği
- Bilgi paylaşımı
- Ürün akışını düzgünleştirmek
- Parekedencilerle koordine olarak teslimatları eşit yaymak
- Bir defada işlem gören miktarı aşağıya çekmek
- Küçük miktarda ve yüksek sıklıkta ikmal
- Sistem bozucu teşvikleri devre dışı bırakmak
- Her gün düşük fiyat politikası
- Geri dönüşleri ve iptalleri kısıtlamak
- Kısa kalma durumunda, mevcut durum yerine geçmiş satışları baz alan sipariş tahsisi
Ayrıca bakınız
- Beer Distribution Game
- Forrester effect mapping
- PID controller
- Supply Chain Management
- Under-damping
Kaynakça
- ^ Managing a Supply Chain is Becoming a Bit Like Rocket Science (2002, Jan. 31), The Economist
Literatür
- Bray, Robert L., and Haim Mendelson. "Information transmission and the bullwhip effect: An empirical investigation." Management Science 58.5 (2012): 860-875.
- Cannella S., and Ciancimino E. (2010). On the bullwhip avoidance phase: supply chain collaboration and order smoothing. International Journal of Production Research, 48 (22), 6739-6776
- Chen, Y. F., Z. Drezner, J. K. Ryan and D. Simchi-Levi (2000), Quantifying the Bullwhip Effect in a Simple Supply Chain: The Impact of Forecasting, Lead Times and Information. Management Science, 46, 436—443.
- Chen, Y. F., J. K. Ryan and D. Simchi-Levi (2000), The Impact of Exponential Smoothing Forecasts on the Bullwhip Effect. Naval Research Logistics, 47, 269—286.
- Chen, Y. F., Z. Drezner, J. K. Ryan and D. Simchi-Levi (1998), The Bullwhip Effect: Managerial Insights on the Impact of Forecasting and Information on Variability in a Supply Chain. Quantitative Models for
- Disney, S.M., and Towill, D.R. (2003). On the bullwhip and inventory variance produced by an ordering policy. Omega, the International Journal of Management Science, 31 (3), 157-167.
- Herlyn, W., "The Bullwhip Effect in expanded Supply Chains and the Concept of Cumulative Quantities", in: Blecker et al. (Eds.): "Innovative Methods in Logistics and Supply Chain Management", p. 513-528, epubli GmbH, Berlin, 2014, ISBN 978-3-8442-9878-9
- Lee, H.L., Padmanabhan, V., and Whang, S. (1997). Information distortion in a supply chain: the bullwhip effect. Management Science, 43 (4), 546-558.
- Lee, H.L. (2010). Taming the bullwhip. Journal of Supply Chain Management 46 (1), pp. 7–7.
- Supply Chain Management, S. Tayur, R. Ganeshan and M. Magazine, eds., Kluwer, pp. 417–439.
- Selwyn, B. (2008) Bringing Social Relations Back In: (re)Conceptualising the 'Bullwhip Effect' in global commodity chains. International Journal of Management Concepts and Philosophy, 3 (2)156-175.
- Tempelmeier, H. (2006). Inventory Management in Supply Networks—Problems, Models, Solutions, Norderstedt:Books on Demand. ISBN 3-8334-5373-7.